Warehouse Management Systems: The Key To Improving Operational Efficiency & Customer Experience
As organizations begin to utilize advanced technologies, warehouse management systems continue to lead in operational efficiency.
Updated on: 2/26/2025
Key Takeaways
- Comprehensive System Integration: Modern warehouse management requires integrated systems that handle multiple functions – from receiving and inspection to order fulfillment and returns – while providing real-time visibility across operations.
- Operational Efficiency Focus: Successful warehouse management combines optimized physical layout, standardized workflows, and automated processes to improve efficiency, reduce errors, and enhance customer satisfaction.
- Technology-Driven Solutions: WMS software and automation are crucial for addressing common challenges like inventory management, labor costs, and space utilization while providing access to real-time data for better decision-making.
Digital technology has transformed the way that customers make purchases. Consumers want the ability to purchase, fulfill and return products quickly and with as few steps as possible. A smooth warehouse management system enables organizations to control and administer warehouse operations from the time that materials and goods arrive at the warehouse to the moment they are sent to recipients.
Warehouse management solutions enable companies to optimize their warehouse and distribution center operations to achieve a range of benefits, such as improved operational efficiency and customer experience. A warehouse management system (WMS) is an innovative software solution that provides greater visibility into a company’s inventory and helps in the management of supply chain fulfillment operations.
01
Chapter 01
An Introduction To Warehouse Management System Software
What is warehouse management software and how is it used to improve operational efficiency in the retail and manufacturing industries?
With a warehouse management system, organizations can accurately track materials and goods as they arrive and leave the warehouse. These systems also streamline how workers receive, inspect, pick, store and pack orders.
How A Warehouse Management System Works
Warehouse management systems contain a wide range of information designed to optimize warehouse processes. When a customer places an order, the system can immediately determine if the products are available by reviewing the current inventory. If the products are found in stock, the system will mark the order as ready for packing. These automated processes can save workers a significant amount of time and effort.
There are several types of warehouse management systems. The most popular include standalone systems, supply chain modules, ERP modules and cloud-based systems.
Standalone Systems
A standalone system is one of the most affordable types of warehouse management systems but also the most basic when it comes to features and capabilities. These systems are a typical on-premise solution that is used with an organization’s original network and hardware. Standalone systems are typically purchased without advanced supply chain functions and only include the most important features of WMS modules.
Organizations can expect to take advantage of these features of a standalone warehouse management system:
- Barcode scanning
- Expiration date tracking
- Inventory cycle counting
- Inventory put-away
- Inventory slotting
- Receiving of goods
- Product picking
- Product packing
- Product shipping
Many newly established or small businesses with tight budgets use standalone warehouse management systems due to greater accessibility. Standalone systems can be used as one-off software, inventory management systems or a combination of other essential system integrations. However, they do not incorporate other steps of the logistics chain.
Supply Chain Modules
Supply chain modules are broader in scope than standalone systems and can help customers better manage various aspects of supply chain visibility. The primary goal of supply chain management (SCM) is to optimize and automate the monitoring of inventory cycles, inventory replenishment, material acquisition and other routine tasks. Supply chain modules also allow for the accommodation of risk analysis, vendor partnerships and current market activities.
Organizations that choose to invest in supply chain modules must be willing to purchase supply chain planning applications that provide additional warehousing features. Combining warehouse management systems with other applications is an excellent way to achieve cohesion between various components of the business. Supply chain modules support holistic management of the entire supply chain, compared to standalone systems that only cover warehousing.
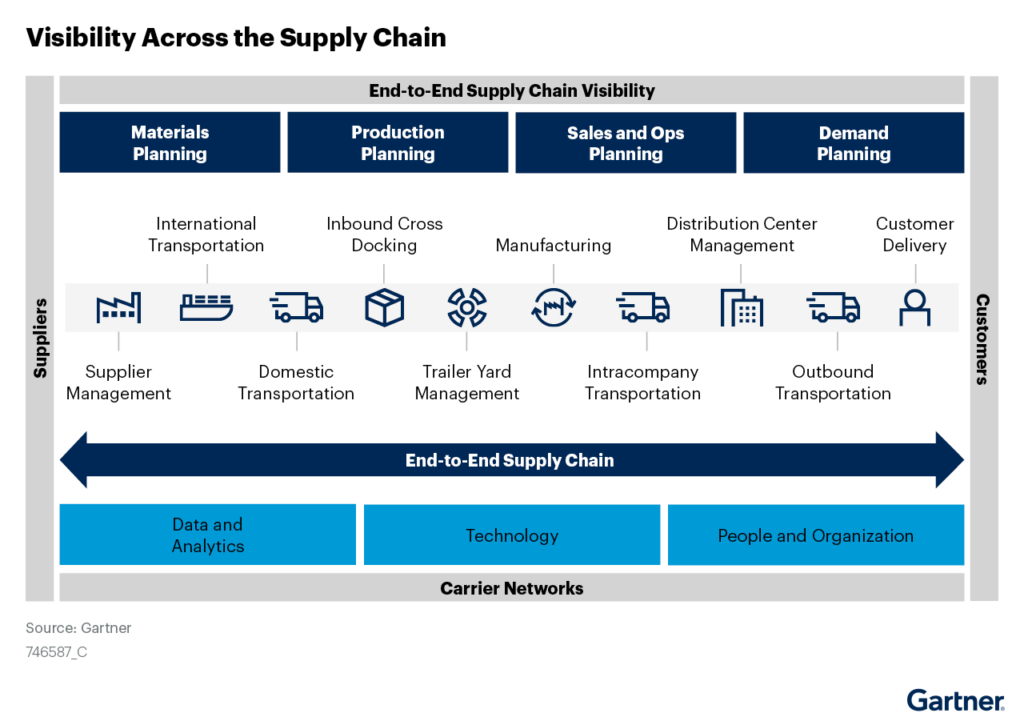
Figure 1.1 provides a visualization of how supply chain modules within a custom warehouse management system can show complete visibility of the entire supply chain. A recent study by Gartner provided valuable insight into how many supply chain organizations are now prioritizing visibility and transparency in the transportation process of their supply chain[1].
Business leaders that choose supply chain modules must create a strategy to avoid overlaps with their existing software. This can be achieved by combining different software solutions into a single SCM platform or by choosing an SCM solution that integrates with other critical business software, such as ERP or payroll systems.
ERP Modules
Enterprise resource planning (ERP) modules refer to software that tracks a company’s resources. This WMS solution offers core applications like sales, marketing, accounting and human resources software systems.
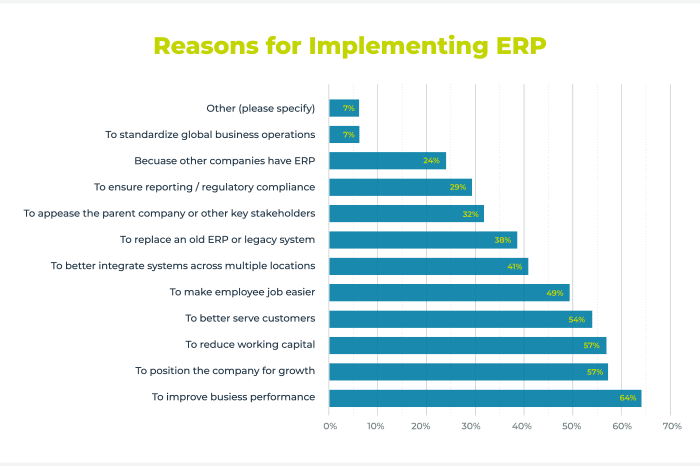
ERPs can be a powerful software option for organizations that want to combine the capabilities of many different systems. From supply chain planning to customer relationship management, ERP modules are ideal for companies that want to upgrade their software strategy on a larger scale.
WMS as an ERP integration is different from standalone systems as they provide warehouse management as a component of a tool with broader capabilities. Companies can choose to invest in a specialized warehouse management system or invest in a combined product, depending on their unique business goals.

Read our guide on how to choose the right custom ERP software for your organization to get a better understanding on how ERP software can greatly improve task and process efficiencies.
Cloud-Based Systems
Cloud-based WMS solutions refer to a web-based computing approach that uses cloud technology. This type of warehouse management system is known for its scalability and excellent speed of deployment. With cloud-based solutions, organizations can achieve many of the same benefits as a traditional WMS while enjoying more affordable inventory costs and faster supply chain execution.
As cloud-based systems are web-based, the warehousing application does not require any installation or synchronization with native networks or hardware. This can save businesses a significant sum of money and make it easier for organizations with many different locations to remain connected. Cloud-based systems also help reduce data entry time and optimize other warehouse activities, such as inventory reporting.
Implementing a cloud-based warehouse management solution enables companies to manage several different system functionalities from a single, convenient system. This ensures the prompt release of product updates and provides workers with real-time access to critical data.
Warehouse Management System Key Components
The modern retail environment focuses on providing excellent customer service. Today’s customers expect rapid fulfillment and are less tolerant of late shipment and transaction errors.
According to Deloitte data, 81 percent of consumers read reviews and check business ratings when making purchasing decisions[2]. Making too many mistakes could put a company at risk of reduced sales.
Great customer service relies on a well-run warehouse. Developing a strong warehouse management system requires extensive planning, attention to detail and the optimization of all key components.
The core components of a warehouse management system include:
- Receiving & Returns – Warehouse management systems record the receipt of stock and returns within a warehouse facility. A WMS helps prevent oversells and out-of-stock scenarios by maintaining real-time quantities of products.
- Warehouse Logistics – A warehouse inventory system can help model and manage the logical representation of physical storage facilities. This is an area where a WMS can significantly improve efficiency.
- Integrations – Enabling a seamless link to logistics management and order processing can help companies pick, pack and ship out products efficiently.
- Reporting & Forecasting – Warehouse management systems allow for the efficient tracking of product locations, storage and supply chains. With reporting and forecasting tools, companies can make more informed decisions based on the latest data.
How WMS Works In Last-Mile Delivery
The connection between a organization’s warehouse management system and last-mile delivery is not always clear. In most cases, last-minute delivery is handled in the transportation management system (TMS). Regardless, a WMS plays a key role in ensuring that deliveries are handled smoothly and with as few delivery errors as possible.
There are several ways in which WMS plays a role in last-mile delivery. Some critical WMS functions in last-mile delivery include:
- Load Sequencing – Although route planning does not occur in the WMS, route plans should always be considered during loading to ensure that the correct loading plan is followed to deliver goods to customers in the most efficient way.
- Integrations – All systems within a tech stack must be properly integrated with one another to function at an optimal level. Data needs to efficiently flow back and forth without interruptions to deliver a real-time view of the supply chain.
- Inventory Management – A warehouse management system is often used as items are loaded and delivered to keep track of inventory, including what products are still in the warehouse and which have gone out for delivery.
02
Chapter 02
The Strategic Role Of Warehouse Management In Supply Chain Operations
Warehouse management systems are designed to manage a variety of important fulfillment processes in supply chain operations.
With efficient supply chain management, organizations can maintain an uninterrupted flow of goods, starting from the gathering of raw materials to the distribution of goods.
Many different factors can disrupt the supply chain and cause delays in deliveries. When organizations take advantage of the innovative tools and features available through a WMS, they can significantly reduce these risks and improve the customer experience. Here is a look at the top seven strategic responsibilities of warehouse management in supply chain operations:
1. Receiving & Inspection
Proper warehouse management begins with the receiving and inspection of raw materials that arrive at the warehouse. Employees are tasked with inspecting pallets of inventory and checking products received by suppliers or vendors to ensure that the materials have not been lost or damaged during transit. If discrepancies occur with inbound products, they must be quickly resolved by placing a new purchase order.
Warehouse management systems can help optimize inbound and outboard logistics. The right software solution enables companies to track the location of equipment and inventory as it moves throughout the warehouse. Warehouse management begins as soon as the warehouse expects to receive inventory by providing employees with inbound planning tools, such as optimized scheduling.
2. Product Storage
Once received and inspected, warehouse employees transport the materials to a designated location within the warehouse. This is the location where the products will be stored until they are ordered by customers. Organizations must use extreme caution when choosing a place to store goods as products must remain secure and in a temperature-controlled environment. In addition, products must be handled with care to prevent damage to inventory.
Warehouse layout and storage allocation can have a dramatic impact on order processing times, especially in larger warehouses. Having a well-designed WMS can help organizations reduce their operating expenses.
This software solution determines the most effective use of space and labor to minimize waste. In addition, a warehouse management system enables organizations to create floor plans to best determine where to store certain products and materials.
3. Order Picking and Retrieval
Once the inventory has been properly stored, it is a picker’s responsibility to retrieve orders from storage as they are made by customers. Pickers must work quickly and with a high rate of accuracy to ensure that the right product, including the appropriate product size and color, is retrieved and brought to the packing location.
Enhanced visibility is one of the biggest advantages of introducing a warehouse management system. WMS software allows pickers to access real-time data on available inventory through serial numbers, barcoding and RFID tagging.
In addition to helping pickers find the right item, a WMS can be useful in forecasting. Data can provide valuable insight as to what products are most popular among customers during certain times of the year.
There are several types of order picking processes that businesses may implement, including:
Discrete Order Picking
The most common order picking method is discrete order picking as it is simple and easy to understand. With the discrete order picking method, an order-picker picks a single order, one line at a time. In addition, this method involves only one order scheduling window during a shift. This means that orders are not scheduled and can not be picked up at any time of the day.
There are multiple advantages to this method, such as simplicity, faster response for order fulfillment and easier tracking of order picker accuracy. Discrete order picking is also the ideal method for paper-based picking. While simple, discrete order picking is considered the least efficient method as it involves significantly more travel time compared to other methods.
Batch Order Picking
Also referred to as multi-order picking, the batch order picking method enables pickers to work on multiple orders at once, one SKU at a time. This method is best suited for companies that frequently encounter multiple orders with the same SKUs or orders that have just a few SKUs in each.
Batch order picking allows organizations to significantly cut down on travel time as pickers generally only need to travel to an item location once per picking cycle. This method is ideal when the SKUs’ physical dimensions are relatively small or the average order profile has just a few SKUs, typically under four. Batch order picking is similar to zone order picking as it only requires one order scheduling window for each picking shift.
Wave Order Picking
The wave order picking method requires pickers to work within assigned zones. All zones are picked from simultaneously, instead of having one zone that is passed onto another, which helps to save time. The items are then sorted by employees and consolidated into the proper shipments.
This method is similar to the discrete picking method in that one picker picks an order, one SKU at a time. The biggest difference between them is the scheduling window. With discrete picking, there is no scheduling window while in wave order picking there is a scheduling window.
Wave order picking is typically faster as employees do not have to wait for each zone to perform their responsibilities before the order can transition to the next zone. However, this method may require more time and employees to navigate the sorting and consolidation process. Wave order picking is best suited for companies that possess a high number of picks per order.
Zone Order Picking
Zone order picking is a type of order picking method usually combined with other methods, most commonly the pick and pass method. With the pick and pass method, the warehouse is divided into several zones with employees assigned to each zone.
Associates pick SKUs for several orders at a time within their zone and then pass them to the next zone. The term pick and pass is often used interchangeably with zone picking but there is a difference. Zone picking can be carried out without passing containers or bins from zone to zone.
With zone order picking, a warehouse is divided into multiple zones and each picker is assigned a specific zone from which to pull items. When orders require products from multiple different zones, the order container is passed to the next zone and the pickers continue picking items for the order until the order is complete. Zone order picking is best suited for companies that run high-volume warehouses and often encounter picker congestion in certain areas.
Cluster Order Picking
Cluster picking is the method of picking into multiple different order containers at the same time. These containers may be totes that contain order batches, discrete order totes or discrete order shippers. There are two main picking systems that can benefit from using the cluster picking method. These cluster order picking systems fall under the manual or automated picking options:
- A pick-to-cart operation occurs when a cart is loaded with multiple shippers or totes and the picker makes a pass through the pick zone to sort through containers. This option helps to cut down on travel.
- A vertical lift module (VLM) operation uses the independent zone picking technique in which a picker sets up a pick container batch and initiates mechanized pick modules. The items are then sorted into the proper containers.
4. Packaging Items
Packaging has made great strides over the last several decades, transitioning from the movement of basic envelopes and boxes to complex systems that allow products to move swiftly along a global supply chain. Safe, cost-effective and well-designed packaging is a must in the industry, forcing many companies to find new ways to package more efficiently.
There are many important elements of packaging, including how the package is designed, the specifications of the package and ergonomic considerations. As supply chains become more robust, there has been a greater focus on developing a more organized process for packaging, such as enhanced labeling and traceability. Sustainability also comes into play as many businesses focus on waste prevention and limiting the use of certain processes and materials.
5. Transportation Of Goods
The supply chain relies on the effective management of logistics and assets to ensure that raw materials, parts and finished products are safely transferred from one location to another. When transporting goods, organizations must ensure their usage of vehicles, containers and other assets are optimized for effective logistics execution.
Trucks are primarily used in the international supply chain. Along with railways, trucks are the primary way to move goods across long distances in the most efficient manner possible. Most commercial trucks are fitted with chassis to hold standardized shipping containers.
Once the goods have been picked and packed, a warehouse management system can send itemized bills of lading (B/L) before the shipment, generate invoices and packing lists for buyers and assemble instructions if needed. A WMS can also send advanced shipment notifications (ASN) to alert other facilities of pending deliveries.
Long Distance & International Transportation
Last-mile delivery refers to the transportation of goods from the warehouse to a customer. In some cases, the customer is located a long distance from the warehouse or possibly in another country. When it comes to long-distance and international transportation, organizations must take extra precautions to keep goods safe and free from damage while in transit.
For long-distance and international transportation, warehouses generally form relationships with several different couriers, such as FedEx, UPS, USPS, Freight Air and in some cases, railroad transportation. The mode of transportation chosen depends on several factors, such as the size of the item being shipped and customer preference.
Organizations rely on warehouse management systems to get orders into the hands of couriers safely and track information associated with an order to the appropriate customer soon after the goods are shipped. With a WMS, organizations can maintain good customer service while keeping all parties informed on the status of packages in transit.
Local Order & Smaller Territory Transportation
Some companies wish to avoid the risk of poor customer service from third-party couriers by gathering their own team of couriers to deliver goods and provide excellent customer service. This is often achievable by companies that only need to deliver local orders or engage in smaller territory transportation.
With local order and small territory transportation, organizations can choose self-delivery as their go-to for last-mile delivery. Along with putting together a team of reliable couriers to make the deliveries, organizations will need to purchase and integrate delivery management software that will help them better manage delivery routes.
There are countless advantages of keeping the final transportation stage of the supply chain in-house, including greater control over when and how goods are delivered to customers.
6. Auditing & Inventory Control
Auditing and inventory control are important elements in warehouse management. Auditing is the process used in warehouse inventory control and quality assurance (QA) to ensure that any damaged products or small inventory errors do not turn into larger and more costly problems.
Warehouse managers are generally tasked with performing audits at various frequencies, depending on the overall size of the warehouse and the complexities of the operating floor. In most cases, auditing involves comparing current inventory levels with data found on the warehouse management system to ensure that all information aligns. This method can also be useful for inventory forecasting.
During an audit, managers may check products that contain expiration dates to ensure that there are no goods that have surpassed their shelf life and need to be disposed of or replaced. Auditing processes may also include assessing personnel, scheduling strategies, product layouts and other elements of daily operations.
7. Returns & Restocking
A couple of areas where companies often fall behind are returns and restocking. These critical elements of warehouse management directly impact customer service and help ensure that customers’ orders are delivered as quickly as possible.
It is the responsibility of warehouse personnel to provide customers with a seamless and effective reverse logistics or ‘return management’ process within the supply chain. Regardless of how great a company’s products are or how well they are picked, packed and delivered, there is always a risk that the product could be returned by a customer.
Warehouse management teams must learn to effectively handle receiving and possibly restocking products that are returned, as well as picking and packing new goods for customers who request exchanges. A warehouse management system can help make these processes more efficient by notifying employees when a return or restocking is needed.
03
Chapter 03
Common Warehouse Management Challenges
Warehouse management can be complex as systems coordinate a series of processes that must work together seamlessly to maintain a high volume of customer orders.
Since the start of the COVID-19 pandemic, warehouses have gone through significant changes to keep employees safe, maintain profitability and fulfill customer orders as quickly as possible.
Despite their best efforts, warehouses are likely to encounter challenges in warehouse management that affect their ability to deliver, as well as their bottom line. Organizations are tasked with handling many critical elements at once, such as making the best use of available warehouse space, managing employees effectively, adapting to seasonal demands and similar issues that may develop over time.
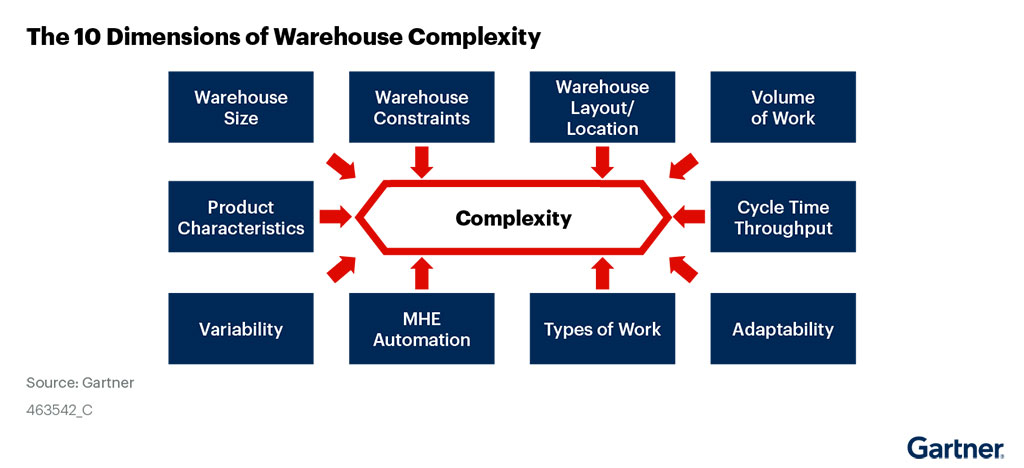
According to Gartner, there are 10 specific dimensions of warehouse complexities[3] that should be evaluated when considering what features and functionalities a custom warehouse management system should be able to handle, as shown within Figure 3.1
Here is a closer look at some of the most common warehouse management challenges experienced by modern businesses and how they could affect a company’s operations.
Inventory Management
Organizations that fail to develop a proper inventory management system can run into problems, such as incorrect amounts of stock. Employees may go to a particular location to pick stock for an order only to find that the product is not available.
Employees can also run into similar problems when stocking items in a location that is already full due to wrong inventory data. Inaccurate inventory management can cause a wide range of issues that lead to wasted time and money.
Companies that rely on manual processes of updating inventory are at a high risk of encountering improper stock information. Employees in these situations are often forced to spend considerable time performing physical inventory checks and making corrections in the system.
Unoptimized processes can waste valuable time that could be better spent performing core activities that help grow the business. A robust inventory management module can help automate these important processes and eliminate costly errors.
Facility & Space Layout
Many organizations overlook the importance of proper facility and space layout. A poorly configured warehouse can cause a range of challenges in terms of proper inventory management. Many warehouse managers struggle to maintain efficient processes when their facility and the space layout are not as optimized as they could be.
According to a recent Warehouse/Distribution Center Equipment Survey, the average warehouse capacity utilization is just 68 percent[4], meaning that many warehouse spaces are not being efficiently utilized.
When warehouses are not properly set up, it can also result in time waste. Employees often spend more time searching for products and poor space layout can cause pickers to spend more time than necessary finding the product they need, resulting in fewer orders being fulfilled.
Picking Optimization
When an order is placed by a customer, pickers are assigned the task of completing the order. Unfortunately, substandard picking processes can lead to wasted time and money in warehouses. If the picking process is not effective, pickers spend more time than necessary fulfilling an order.
When inventory issues or delays are involved, this can extend the process even more. Organizations are unable to fulfill enough orders in a day, resulting in a backup of unfilled orders. In turn, customers are unhappy and the rate of canceled orders increases.
A large majority of a picker’s time is spent moving around the warehouse but not necessarily picking products.
Warehouse management should be approached in a way that helps minimize the amount of movement performed by pickers. This requires organizations to create a better inventory layout and implement automation systems that increase picking efficiency and reduce errors.
Labor Costs
Labor costs can make up a significant portion of a warehouse’s total budget. As an integral component of any warehouse, laborers must be managed effectively to maintain optimal productivity across all warehouse processes.
In a typical warehouse environment, there is staff ranging from on-the-floor associates to higher management. With a range of personnel to manage, along with the management of costly equipment, managing a labor force can prove highly challenging.
One of the most important responsibilities of a warehouse manager is to make important decisions that dictate how to get the most from the available workforce. Organizations can help boost productivity by implementing automated systems whenever possible.
Automated systems can help reduce labor costs and make the overall order fulfillment process faster and more efficient. The use of a comprehensive warehouse management system is key to keeping labor costs under control.
Customer Experience
Many warehouses have hundreds or even thousands of orders coming in and out daily. How these orders are managed can play a critical role in a customer’s experience with a particular company. One mistake an organization can make when dealing with a large influx of orders is to overlook quality assurance.
When workers overlook important details when picking, packing or shipping orders, customers can receive incorrect, poorly packaged or damaged goods. Proper quality assurance is necessary to reduce the risk of poor customer service and the hassles associated with returns.
Having a robust warehouse management system in place has been proven to significantly improve customer experience by automating many vital tasks, such as paperless picking and multi-channel order management. Warehouses can run more smoothly, enabling organizations to serve customers at a level that meets or exceeds their expectations.
See How Orases Was Able To Improve Next Day Dumpsters Customer Experience
Watch Next Day Dumpster’s testimonial, explaining how Orases was able to develop a custom management solution to track customer orders and features which allowed NDD to follow up with their customers after the order was completed.

Read how our custom software development software services helped Next Day Dumpsters scale their CRM to greatly improve task and process efficiencies.
04
Chapter 04
Strategies To Improve Warehouse Management
Running a warehouse is a tough job, no matter how large the space or workforce is. However, getting it right can have a tremendous effect on the organization’s success.
Improving warehouse management can help drive productivity and efficiency, help employees remain safe on the job, reduce overheads, and improve customer satisfaction and profitability.
To improve warehouse management, businesses must adopt strategies designed to reduce waste, automate processes and create overall efficiency across the work environment. This may mean reducing time spent loading and unloading vehicles, ensuring that stock is replenished in a timely manner, and spending less time picking and retrieving stock.
When developing strategies to improve warehouse management, it is important to consider how changes in a warehouse will impact customer experience. Today’s consumers expect a smooth order process that involves the fast processing and delivery of goods without delays or errors. Here is a look at some of the strategies used to improve warehouse management:
Optimize Warehouse Storage & Layout
Organizations require a well-optimized warehouse layout and storage system to ensure that employees are able to store, pick, pack and transport items as efficiently as possible. Properly organizing a warehouse can maximize the number of goods that the warehouse can store. For example, organizations that invest in more narrow equipment are able to set up racking closer together to allow more products to be stored in a tight space.
A robust warehouse management system offers a wide range of features and tools designed to help organizations optimize their warehouse storage and layout. The right WMS enables employees to easily locate items based on their sell-by date, retrieve goods as orders are made, and pack and ship items quickly, resulting in lower inventory holding costs. A well-optimized warehouse also reduces the potential for lost or damaged inventory, saving organizations money.
Improve Labor Management & Productivity
When an organization’s warehouse management system is suffering, labor management and productivity are usually the next areas to encounter challenges. An inefficient, slow or unproductive warehouse operation will often lead to more frequent issues, such as a lack of staff motivation and outdated processes that affect daily operations. Implementing a comprehensive warehouse management system can help improve labor management and productivity in warehouses.
Warehouse management systems can help optimize stock flow by using an automated replenishing system designed to top up stock. When picks are scanned, they are effectively linked to the software where the information is copied to transfer notes or invoices.
To improve labor productivity, it is important to choose a user-friendly system that will not add to employee stress. The platform should possess vast capabilities but still be intuitive and guide users throughout the processes to allow for easy learning.
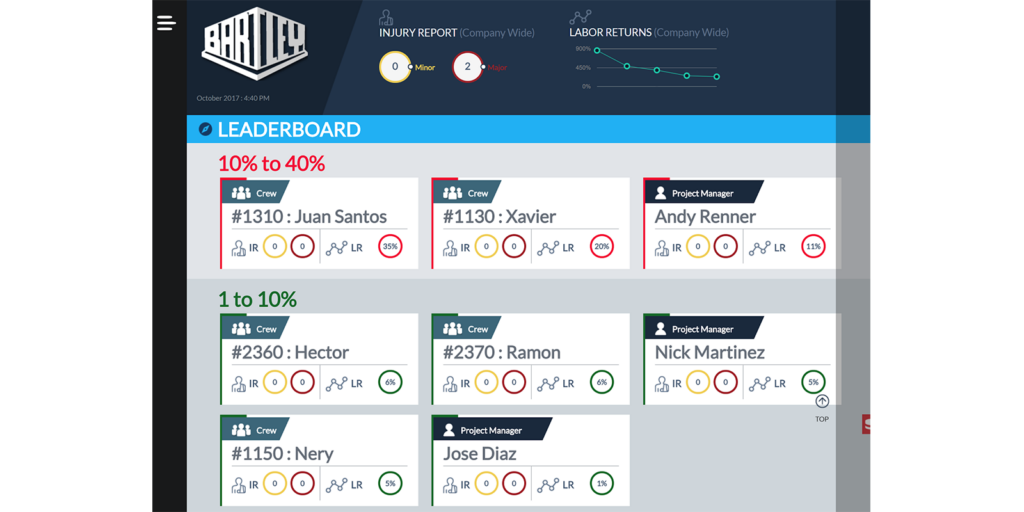
The custom warehouse management system development team at Orases built an employee dashboard for The Bartley Corporation, which enabled them to calculate each worker’s efficiency, and rate them against other employees.
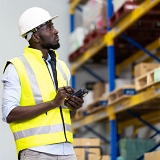
Read how Orases helped Bartley Corporation improve worker efficiency by developing a custom warehouse management system.
Design a Standardized Workflow
When a warehouse lacks a standard workflow, employees tend to work at a pace that they are comfortable with, which may be slower than average. Unfortunately, differences in work habits across a workforce can directly impact operations as some employees may perform their duties faster or more efficiently than others. No standardized workflow also makes it more challenging to measure an employee’s individual performance against established benchmarks.
Every company should establish a standardized workflow to ensure that all employees work within the same specified guidelines. A standardized workflow also helps maintain transparency among employees during daily operations, such as the moving of packages, order fulfillment and other important processes.
When warehouse managers have a well-defined process to look upon for guidance, they are better equipped to identify possible errors or bottlenecks that could be negatively impacting the warehouse’s workflow.
Leverage Automation & WMS Software
Growth-oriented organizations know the importance of investing in warehouse management system software to work faster, be more productive and eliminate common errors.
WMS software can be useful for automating a wide range of time-consuming tasks while providing organizations with greater control in many areas, such as receiving, storage, order fulfillment and shipping. Opt for a WMS that will align with the organization’s current processes and optimize them to achieve maximum efficiency.
WMS software can be useful in many different areas of warehouse management. For example, it can greatly improve inventory management through automation. Warehouse management systems focus heavily on the organization and optimization of inventory storage and tracking.
WMS can also enhance storage space utilization, increase the speed of operations, provide a real-time view of inventory and deliver accurate inventory information. When organizations utilize a WMS to achieve visibility into people, places, products and processes, they become a more profitable and efficient warehouse.
05
Chapter 05
Optimizing Your Warehouse Operations With WMS Software
Warehouses experiencing the rapid growth stage can benefit significantly from a warehouse management system (WMS).
Any organization that deals with inventory coming in and going out can enjoy enhanced operational efficiency, in addition to maximized physical warehouse space, when they implement a WMS. With the right software, business leaders can monitor their company’s workflows and performance across all worksites and levels of operation.
Implementing an automated WMS solution also increases overall productivity in a warehouse environment. It is also the ideal approach to increasing asset utilization and improving inventory accuracy.
Once a warehouse management solution has been implemented, organizations often find that they waste far less storage space and experience a decrease in the amount of time it takes to locate products. In turn, companies can lower their production overhead and increase their profitability.
Improved Inventory & Stock Management
Warehouse inventory management system tools help organizations in tracing and managing warehouse stock as it is purchased, produced, stored and utilized. The system also helps in matching product supply with demand fluctuations. In other words, inventory and stock management software focuses on the entire product lifestyle, from purchase and selling to last-mile delivery of goods.
One of the biggest advantages of introducing a warehouse inventory solution is automation. These types of comprehensive systems can perform low-value, repetitive tasks without the need for human intervention. After setting a command, the process starts immediately. This solution aids in increased stock visibility as levels of inventory are constantly tracked after a sale is made.
Having improved inventory and stock management is not only important for making accurate predictions of supply and demand but also for customer service. With access to automated tools and a wealth of sales data, organizations can prevent unsatisfied customer experiences caused by overselling products that are not available. These solutions provide real-time data meaning once the last item of a particular product is sold, it automatically becomes out of stock in the system.
Access To Real-Time Data For Enhanced Visibility
Having access to real-time data is critical for operational efficiency and good customer service. Warehouse management systems are designed to show results in real-time, allowing business leaders to set up alerts and run reports about the events that are occurring within the warehouse. Event monitoring and real-time alerts also enable internal customer service, customers and partners to gain a real-time view of stock availability and the status of their orders.
Modern organizations aim to deliver exceptional digital experiences to retain their customers and innovate as rapidly as possible. Real-time data warehousing allows for the continuous process of loading data, making it available to the people that need it to perform important functions.
This differs from the traditional data warehouse approach where data would be loaded in batches over the course of a night or on an hourly schedule. Having access to the most up-to-date information can be a game-changer for all organizations.
Logistics Performance Monitoring (KPIs)
Logistics key performance indicators (KPIs) are a common way for companies to compare their own performance against benchmarks in the industry. When businesses track KPIs, they are better equipped to improve their operations, reduce costs, and identify mistakes and address them accordingly.
Businesses often use logistics KPIs to identify improvements that need to be made in the various stages of the flow of goods. The overall importance of these KPIs can vary from industry to industry.
Warehouse management solutions typically offer a logistics dashboard that provides business leaders with a comprehensive view of the company’s metrics. The dashboard may be organized by workgroup, division, topic or another category that makes it easy to see the company’s progress towards metrics and goals.
Ease Of Integration, Configuration & Operation
Many organizations worry about the complexity of integrating a new software solution. With a warehouse management system, there are several ways to implement a new solution within the company.
A fully integrated WMS refers to a solution that is integrated as part of a suite of software tools, such as an enterprise resource planning (ERP) system. In many cases, the fully integrated WMS system will utilize the same configuration and databases as existing systems a company may already use.
A major benefit of investing in a fully integrated WMS is the ease of implementation as there are no complicated integrations that need to be built to allow data to flow smoothly between different systems. This may also mean that the employee training necessary for the new system is faster too.
Reduced Chance Of Errors & Failures
Humans performing tedious and repetitive tasks manually greatly increase the risk of errors and failures within a warehouse. These mistakes can cost organizations a significant sum over the course of a year. While employees are often to blame for common warehouse mistakes, this is not always the case. According to Inbound Logistics, approximately 85 percent of quality issues are attributed to materials and processes[5].
Frequent errors made within a warehouse can have a major impact on the success of a facility. Some of the most common warehouse errors include storing too much inventory, keeping a disorganized warehouse, failure to incorporate technology, poor planning of packing paths and not using technology to its full potential. Warehouse management systems, along with other essential technologies like ERP, have become prominent in larger corporations. However, smaller businesses can also benefit from these innovative solutions.
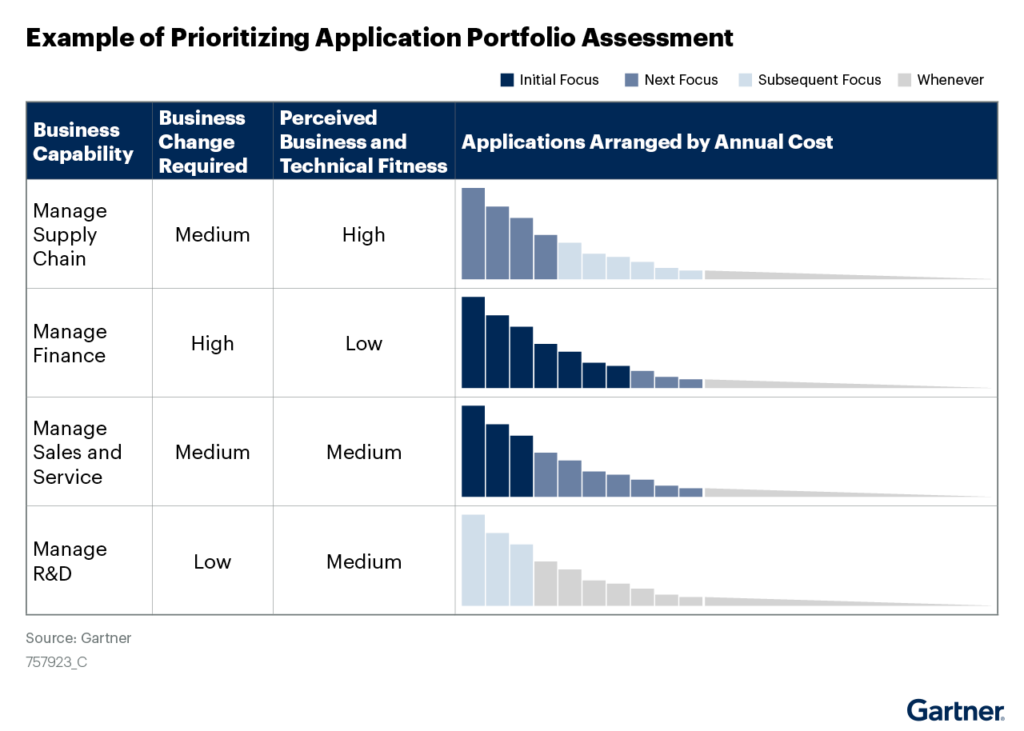
Now you have a better understanding of the benefits a custom warehouse management system can offer your organization, it is now important to review your current organization’s capabilities and level of effort required to improve the proficiency of certain processes and capabilities.
Figure 5.1 provides a visualization as to how organization’s should be both assessing their current capabilities, and the prioritization of features and functionalities of a custom warehouse management system. Gartner provides an in-depth analysis into prioritizing organizational capabilities which need to change for strategic initiatives[6].
Software Solutions That Optimize Supply Chain Fulfillment & Offers Real-Time Visibility
Today, supply chains are more complex than ever. A high-demand market has forced many warehouses to alter their processes and operations to adapt to challenges like higher shipping costs and shortages of vital components. Logistics delays, port congestion and similar issues can directly affect operational efficiency and customer experience.
Modern companies require access to custom software that helps them meet their unique needs and operational requirements. Orases is a leading software company that focuses on building solutions that give businesses a competitive edge. Orases works with businesses in all industries to build software solutions that enable companies to control and administer their warehouse operations in the most efficient and cost-effective way possible.
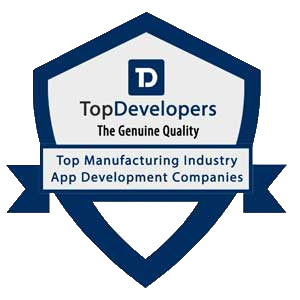
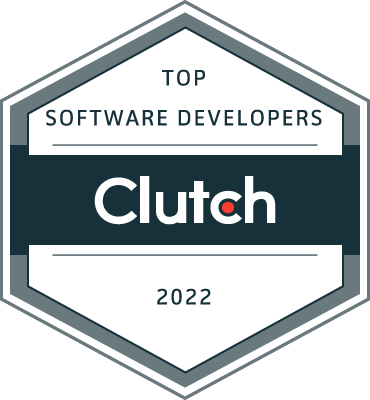
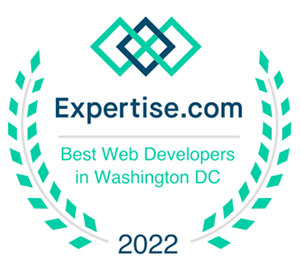
Interested in learning more about developing a warehouse management system? Schedule a no-obligation consultation with a member of the Orases team where we’ll review your vision and develop a personalized approach that is right for your business. Contact us online or call 301.756.5527 to learn more.